HACCP導入「7原則12手順」 (手順10)【原則5】管理基準逸脱時の是正措置の設定
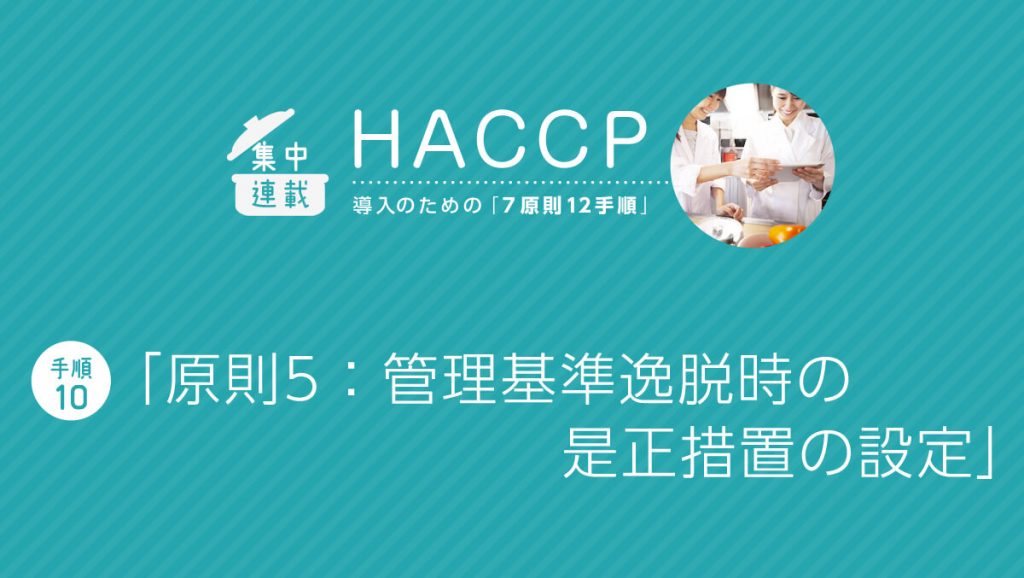
衛生管理手法であるHACCPは、組織全体で適切に実施することが求められます。その際に役立つのが、HACCPの運営手順をまとめた「7原則12手順」です。
近い将来、HACCPが義務化されても焦らなくていいように、各原則・手順についてきちんと内容を把握しておくことが必要となります。そこで、7原則12手順の詳細をそれぞれ解説しました。本記事では、「(手順10)【原則5】管理基準逸脱時の是正措置の設定」について詳しくまとめています。
管理基準から逸脱があった場合に問題点を解決する工程
モニタリングの結果、設定した管理基準(CL)が達成されていないこと(CLからの逸脱)がわかった時に、製造工程の中で発生した問題点をどのように修正し、解決するのかということとその際の記録の仕方について決める工程です。
HACCPシステムの特徴のひとつは、管理基準(CL)からの逸脱を迅速に発見して、影響を受けた製品を排除し、工程の管理状態を元に戻すところにあります。そのため、あらかじめ対処法を規定しておく必要があるのです。
是正措置の設定方法
是正措置を行う目的は、管理基準(CL)から逸脱した原因を特定して工程を正常な管理状態に戻すことと、影響を受けた製品を速やかに特定して排除することにあります。したがって、この目的を迅速に果たせるよう、あらかじめ是正措置を決めて、文書化しておきましょう。
文書については、記録のフォーマットを決めておくと、いざというときにスムーズに改善を行うことができます。
〈是正措置記録の項目例〉
- 製品名
- 管理基準(CL)からの逸脱が発生した工程
- 逸脱した日時
- 逸脱内容
- 調査結果
- 工程に対する措置内容
- 逸脱した製品に対する措置内容
- 是正措置の実施担当者
- 確認者(工場長)
知識があり判断能力に優れた担当者が素早く是正措置を行えるように
管理基準(CL)からの逸脱が起こってしまうのはよくありませんが、もし起こってしまった際にいかに素早く適切な対処をして安全性の高い工程を取り戻し、安全でない製品をきちんと処分できるかということが、食品の安全管理において何より大切になります。
そのため、是正措置の実施担当者には、安全管理の知識が十分にあり、工程をよく理解していて、迅速な判断ができる製造現場責任者などが最適です。担当者には十分な権限を与えておき、管理基準(CL)からの逸脱があった際には一刻も早く是正措置を行えるようにしましょう。
7原則12手順の一覧
- HACCPチームの編成
- 製品説明書の作成
- 用途、対象者の確認(加熱の有無など)
- 製造工程一覧図の作成
- 製造工程図をもとにした現場確認
- 【原則1】危害要因の分析
- 【原則2】必須管理点の設定
- 【原則3】管理基準の設定
- 【原則4】モニタリング方法の設定
- 【原則5】管理基準逸脱時の是正措置の設定
- 【原則6】検証方法の設定
- 【原則7】記録・保管システムの確立
※手順1~5は、原則1~7を進めるための準備となります。